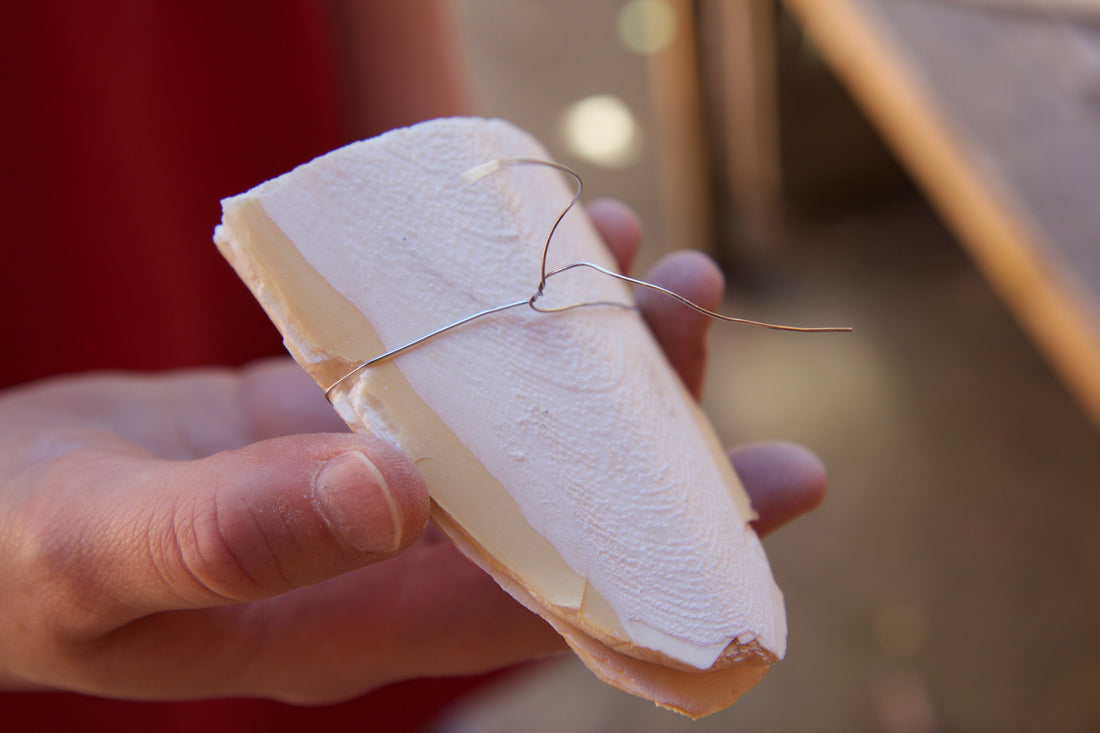
Cuttlefish Bone Casting
I have always been drawn to this ancient method of direct casting. Using gravity and the buoyant structure of the beloved cephalopod, humans are believed to have been casting metal items in this fashion since the 6th century BCE. Made of calcium carbonate, the cuttlefish bone has a soft internal structure that lends itself to carving. Similar to the tufa stone used in the Southwest US, cuttlefish bone is carved to create a negative space that represents the eventual metal object to be cast. Metal is poured directly into the bone, which is cut in half and bound together with wire to create a mold. Multi-part molds are also possible!
The growth pattern of the calcium carbonate creates an incredible texture in the casting: the molten metal picks up every detail from the growth striations. Similar to woodgrain, the structure varies in density leading to unpredictable and delightful imagery. Since no two cuttlefish are alike, no two cuttlefish bone castings are alike. Unlike lost-wax casting, cuttlefish casting often yields only one object, as the bone is charred from the heat of the metal as it is poured into the bone. This singular object, born from a unique method, can then be cleaned and finished like any other metal casting.